Recycling pods: when the defence industry meets the circular economy
If a car is beyond repair, it generally ends up in the scrap yard. For broken toasters, it’s a one-way trip to the waste recycling centre. But what happens to cutting-edge military equipment – packed with components that are scarce, strategically sensitive and potentially harmful to the environment – when it reaches the end of its useful life? Surprising as it may sound in the age of large-scale recycling, the industry does not have a special solution in place for these kinds of products. So until recently, customers often scrapped them, locked them away in a warehouse or simply destroyed them – and not always in ideal conditions. The recycling issue stands at the intersection of three major priorities: ensuring safety and security, protecting the environment and unlocking the economic value of waste. And it’s a challenge that Thales is tackling head-on by setting up a dedicated team as part of its environmental, social and governance (ESG) strategy.
It all started in 2015, when a NATO member country requested a commercial proposal for the dismantling of 40 reconnaissance pods, which Thales had supplied for its military aircraft back in 1993. Before responding to this unprecedented request, Thales first had to check that it was technically and financially feasible.
Cutting-edge systems packed with high-tech sensors
Laser designation and reconnaissance pods are cutting-edge optronic systems packed with high-tech sensors, rare metals, optical and electronic components and circuit boards. Each one measures between two and three metres long, and is designed to be mounted under military aircraft or attached to other combat platforms.
After completing the feasibility study, Thales began dismantling the pods earlier this year at its Élancourt site to the west of Paris. “We're particularly pleased to be working on these systems because some of us helped build them in the past," says a member of the team. "Seeing them return is like coming full circle – although there’s a twinge of sadness in taking something apart when you put so much thought and passion into assembling it.” The members of the dismantling team see their work as an ideal way to reduce our environmental footprint.
Thales is drawing on existing capabilities to develop the new dismantling service, relying largely on a team of a dozen people at Élancourt with experience in handling this kind of sensitive equipment. Supporting the team at Élancourt, Paprec, France’s leading recycling contractor, has all the necessary technical expertise and is also licensed by the French government to work on sensitive systems and technologies.
Some of the most sensitive components need to be handled with particular care, and fortunately the pods were in excellent condition when they arrived at the site. Now it’s up to the engineers and technicians at Élancourt to apply the same care and attention to the dismantling process. “You have to know the product and the precautions to take,” explains the Product Support Manager. “That’s why it’s important for customers to return their pods to the manufacturer at the end of their service life – we’re fully aware of the health, safety and environmental issues involved.” Other components containing rare minerals such as sapphire – or more common materials like aluminium, which are also in high demand – will be recycled using conventional methods.
Once each pod has been dismantled, Thales will provide the customer with a certificate of destruction.
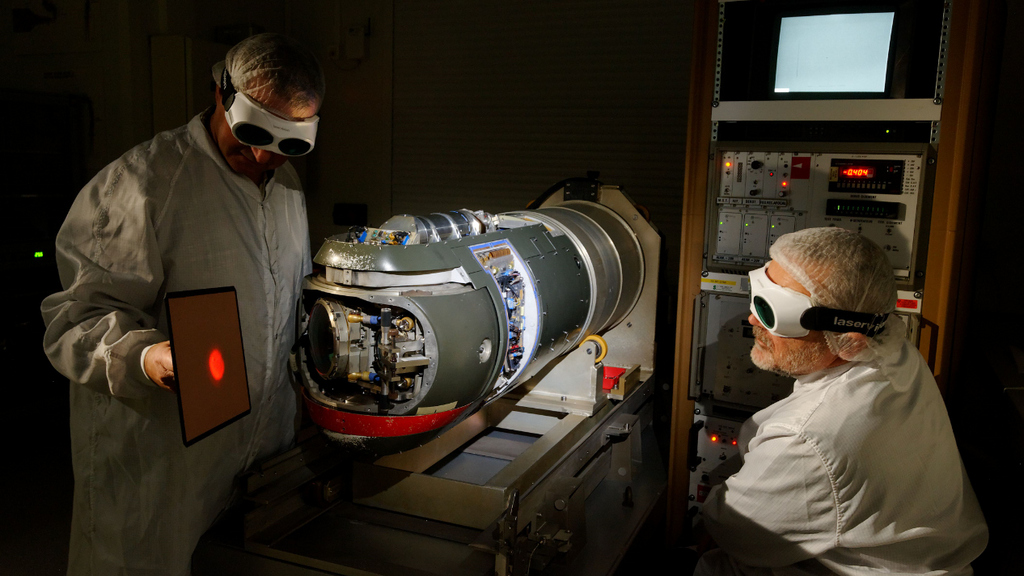
From the battlefield...to the museum
In a new twist, the same customer told Thales in 2021 that it wanted to display five of its decommissioned pods in museums. Although the team at Élancourt had previously made mock-ups for showrooms and trade fairs, it had never turned a working piece of technology into an exhibition piece. It's a meticulous process that involves stripping out every component that could present a public safety and security risk, leaving only an empty shell behind, and then applying a fresh lick of paint to make the pods “museum-ready”. Ultimately, the exercise is a delicate balancing act between keeping the public safe and showing visitors how the systems work.
By catering to a specific customer request, Thales has found a way to develop an additional line of expertise and tap into new business opportunities. Just last year, for instance, the French Air Force asked Thales to submit a proposal for dismantling similar equipment. Other customers around the world are also interested in securely recycling and disposing of obsolete items of equipment, many of which are lying dormant in hangars awaiting destruction. Thales will be submitting its proposal to the French Air Force by the end of the year. “We already have the systems and structures in place, so there’s no reason why we can’t dismantle other products,” points out the Product Support Manager. “All the hardware we supply will eventually be decommissioned and then destroyed or recycled. We already have the capacity to grow this line of business, and over time we’ll be able to add new services to our portfolio.”
The new service further strengthens Thales's leadership in decommissioning management for all of its systems, including military hardware. For a company that has made environmental responsibility a key priority, the strategy has never been more topical or more important.
Eco-design at ThalesAs well as developing a new end-of-life recycling service, Thales is engaging with the principles of eco-design – in other words considering how the environmental impact of its products can be reduced from the earliest stages of the design process. The Group has stated publicly that 100% of its new products and services will apply these principles by 2023. This pledge has been in the making for quite some time now. “We started thinking about eco-design back in 2010,” said Marc Heude, Eco-design Manager at Thales [in an interview in L’Usine Nouvelle published in 2020], "and the process moved up a gear in 2016 when we made eco-design a strategic priority.” Heude added: “The challenge is to limit a product’s environmental impact without sacrificing performance. In fact, these considerations are two sides of the same coin. Our latest assessments show that more eco-friendly technologies often tend to perform better. Things like extending battery life, reducing weight or increasing a product’s lifespan are really just design improvements. Today’s focus on the circular economy is pushing us to optimise everything we can. It’s a powerful driver of excellence in design.” |