Switching from Dates to Data
Credit for the following article goes to Inside Track, Issue 5
Optimising maintenance and operational costs is one of the biggest challenges facing the railway industry. With thousands of assets and employees for operators to manage, in addition to providing a quality passenger service, the careful allocation of time and resources is critical.
Corrective maintenance was and still is, the first maintenance strategy implemented by many industries. This strategy takes a run-to-failure approach that involves waiting until a failure occurs to repair the equipment or component. Although rare, some rail infrastructure companies still take this approach to their maintenance strategy.
Traditionally, scheduled maintenance programmes are how the rail industry has approached keeping networks running. This strategy involves planned interruptions with fixed periods of time for specific asset types. The main objective of this strategy is periodically learning about the condition of assets and preventing unplanned shutdowns. The frequency of these planned shutdowns is normally based upon maintenance and operations experience, and equipment vendor’s advice. Although this method works and it provides a safe environment for trackside workers, it is expensive, incurs costs and requires the time of employees that could be deployed elsewhere, even when it’s not necessary.
Outside of planned maintenance, companies also pay a great price when they cannot manage unplanned shutdowns. Research shows that companies worldwide could be saving as much as €149M per year, if they could avoid unplanned failures. These unplanned failures cause delays to customer journeys and they can originate from many sources. The top contributors to delays to passenger journeys are external causes, such as weather and power failure, as well as signalling failures.
The case, therefore, for alternative ways to manage maintenance on Britain’s railways is clear and in recent years, operators have been moving towards a condition monitoring approach. This approach uses a system to continually monitor the health of thousands of assets on a given network, which presents a number of opportunities for operators to improve efficiency and reduce their costs.
Smarter Maintenance
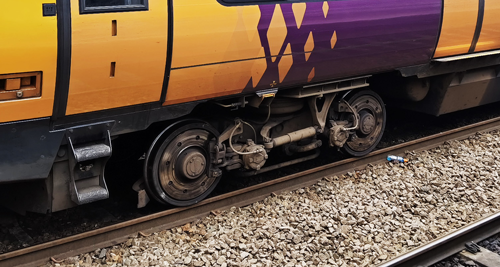
Smart maintenance can be used to mitigate many contributors to unreliability and the benefits of a more intelligent, predictive fault monitoring system can be beneficial to a wide range stakeholders. By understanding and proactively managing the rate at which the assets on a network degrade, it is possible to ensure that passengers experience fewer delays and cancellations due to equipment failures, operators minimize any fines from rail regulators for delays, and the amount of trackside work required is reduced, which frees up operations staff to focus on other tasks.
With the introduction of remote condition monitoring (commonly known as, RCM) techniques, it is possible to retrieve information about the status of thousands of railway assets. The types of assets that can be monitored can range from axle counters, to point machines or track circuits. This extends the potential capabilities of more flexible, time-based maintenance strategies and gives the opportunity to learn how the asset is behaving over the course of a set period of time. Armed with this information, infrastructure owners are able to identify imminent failures and act prior to their occurrence.
Companies that decide to move beyond traditional condition monitoring systems are not only able to identify trends in the behaviours of their assets, but they can also obtain a detailed diagnosis of any problems. Added to this, a more complete view of asset performance can be provided by tracking several variables that can directly influence the failure of a mechanism, such as the age of an asset, its historical usage and any prior faults. By combining all of this data, operators can better understand the health of their assets, which puts them in a stronger position to plan any relevant maintenance and repairs. Through understanding any problems in detail, maintenance workers are able to take only the necessary equipment to perform the repair, which saves both time and cost.
The Long Term Impact
The implementation of a smart maintenance strategy can offer different benefits throughout the lifecycle of an asset. The knowledge acquired throughout the different stages of an asset’s life can be used to support the decision-making process for subsequent projects. The benefits, therefore, span beyond just the immediate return on investment that would come from savings in maintenance expenditure and the avoidance of penalties. They also include the invaluable knowledge that can be acquired for use on future projects, as well as the increased levels of safety achieved through less site visits being needed by the maintenance team.
Apart from indicating the status of an asset’s condition at a specific point in time and offering insights around trends, smart maintenance offers advice on what is the best strategy. These recommendations can only be achieved by extensive industry knowledge incorporated into machine-learning algorithms that consider all the information available. Deep learning, an example of machine-learning techniques, plays an important role in taking all this data and transforming it in potential action-plans to improve reliability and maintenance.
Discover, Predict and Advise
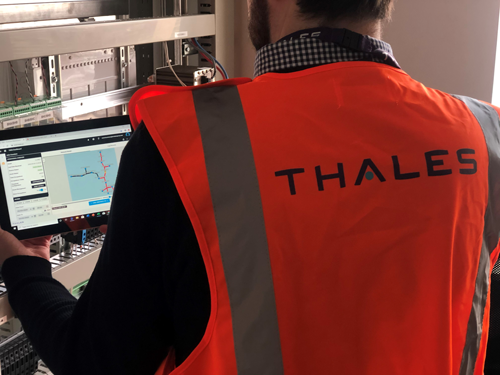
One company already harnessing big data analytics to provide a smart maintenance solution is Thales. Their smart maintenance platform, also known as TIRIS, goes beyond traditional remote condition monitoring methods to discover potential faults, predict when they are likely to occur and advise a corrective course of action. By processing large amounts of data that is normally underutilised by rail operators and maintainers, a solution such as TIRIS is able to streamline and improve upon a maintenance approach that would otherwise take considerably more time and resources to deliver. Data is gathered from a range of assets, such as axle counters, which specifically is achieved by connecting to a Thales system known as ‘AzLM’. Added to this, it can all be carried out remotely, which enables operators to manage their networks wherever they may be.
Network Rail’s Anglia route are one example of operators that are already seeing the benefits of remote condition monitoring. They recently made a pre-emptive repair to a type of critical trackside equipment on the North London line that had previously been causing hundreds of minutes of delays to passengers every month. The repair was guided by Thales’s smart maintenance platform - TIRIS.
The Anglia route installed the innovative cloud based technology in order to identify faults with axle counters before they fail. The digital technology is used to monitor more than 300 axle counter sections on London Overground's North London line and has now been rolled out across the wider route.
Following the installation of TIRIS onto all the axle counters on the North London line, engineers are now able to check the condition of the equipment remotely in real time using tablet devices or laptops. This enables them to carry out maintenance where it’s most needed and fix faults with the axle counters before they start causing disruption.
Increasing axle counter reliability has made a big impact for passengers. Over the last year there has been an average of only one axle counter failure per quarter, compared to an average of two failures per period in 2019, before the improvement programme began. In total, it is estimated that the programme has saved just under 6,700 delay minutes in the last 12 months.
Emma Askam-Johns, Performance Improvement Manager for Network Rail Anglia, said: “We have made rapid progress since we began to focus on axle counter reliability in January 2020."
“The installation of our remote monitoring system is particularly ground-breaking. The North London line is one of the first places in the country to have this type of technology and it is playing a major role in driving down delays for passengers. It also helps us to keep our engineers safe by reducing the number of times they go out on the tracks."
TIRIS has visibly reduced delays and associated costs through decreasing delay minutes and cancellations.
The Journey Ahead
New technologies and methodologies for maintaining Britain’s railways present an interesting alternative for operators. The challenge of improving the efficiency of operations, while also catering to the experience of passengers, is not going to go away over the coming years. The question for operators in our industry, therefore, is whether the long term efficiency improvements and cost savings outweigh the initial short-term cost of implementing new strategies.
Smart maintenance regimes are now cheaper and easier to implement when considering the advent of new technologies such as Industrial Internet of Things, Cloud-enable applications and big data analytics. The benefits of such an approach are also vast – from improving reliability and availability of assets and systems by enhancing the financial performance of rail operations, to supporting improved safety levels.
Time will tell whether more operators will embrace the digital technologies that could transform the maintenance of Britain’s railways. For now, it is clear that there are far more technologically advanced options available than traditional strategies offer and the ongoing development work of such solutions will only continue to further increase the range of possibilities.