“Addictive” manufacturing
How additive manufacturing works
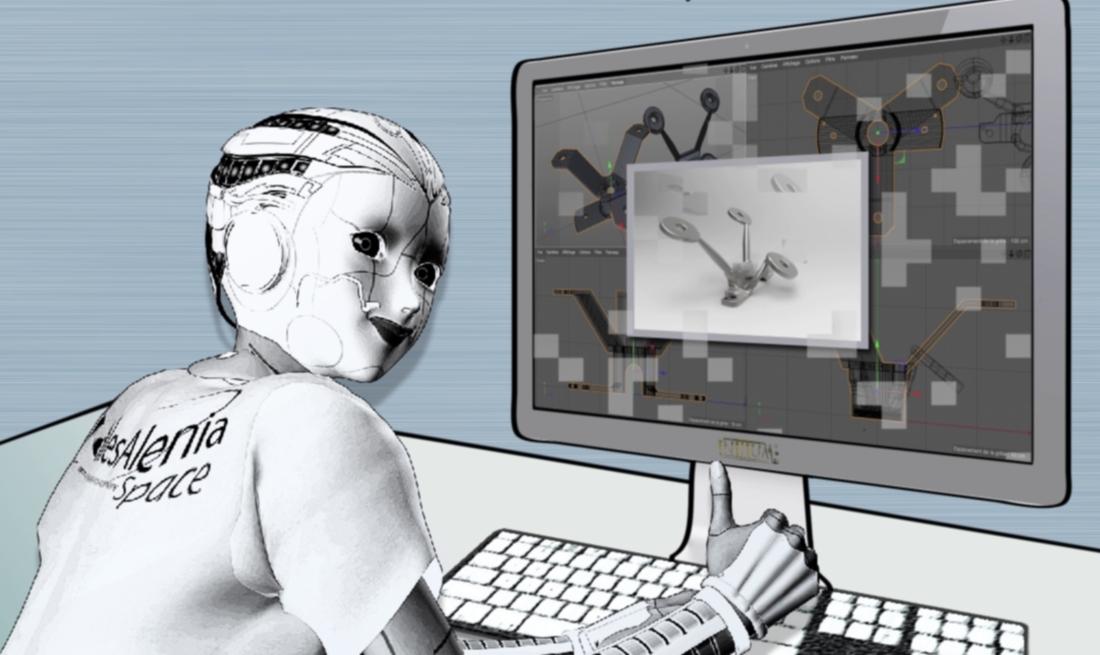
Success Story
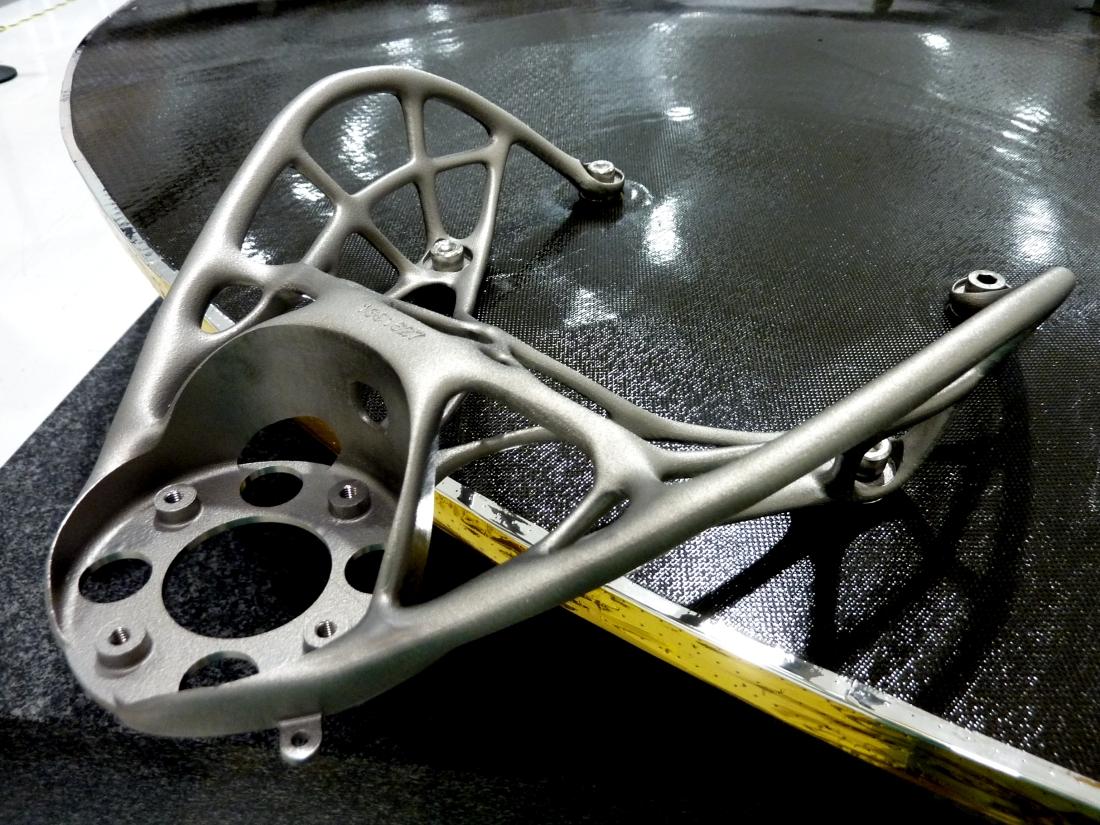
In 2017, 45 communications satellites built by Thales Alenia Space as prime contractor were successfully orbited – and all of them were fitted with 3D-printed parts. It all started a few years ago, when a 3D-printed aluminum antenna bracket was fitted to the TurkmenAlem/MonacoSat satellite, in orbit and operational since 2015. The launch pace really picked up over the next two years, with 45 of our satellites launched in 2017, including 40 for the Iridium NEXT constellation. As a result, the number of 3D-printed parts in orbit beat all previous records. An announcement in 2015 said that that the upcoming Koreasat-7 and 5-A satellites (successfully launched in 2017), would include the largest 3D-printed parts ever made in Europe at the time. In the meantime, the record was broken by the RF (radio-frequency) horn and antenna bracket for the Hellas Sat 3/Inmarsat S EAN satellite launched in June 2017… and the race is far from over. Today, all Thales Alenia Space communications satellites use 3D-printed antenna brackets and reflector sleeves.
Everybody’s doing it!
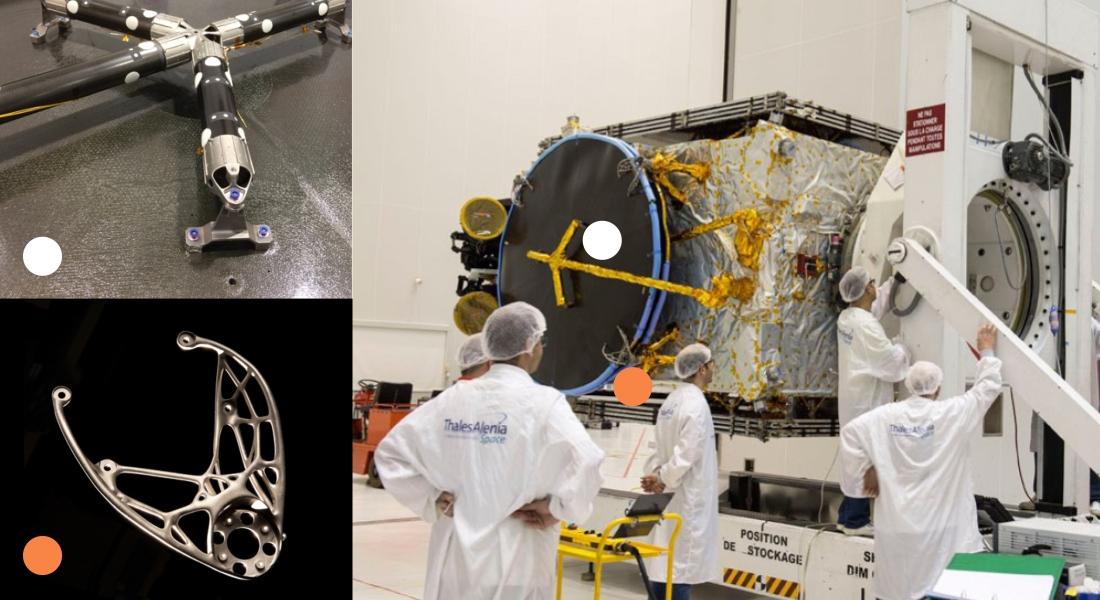
Additive manufacturing for spacecraft: what’s next?
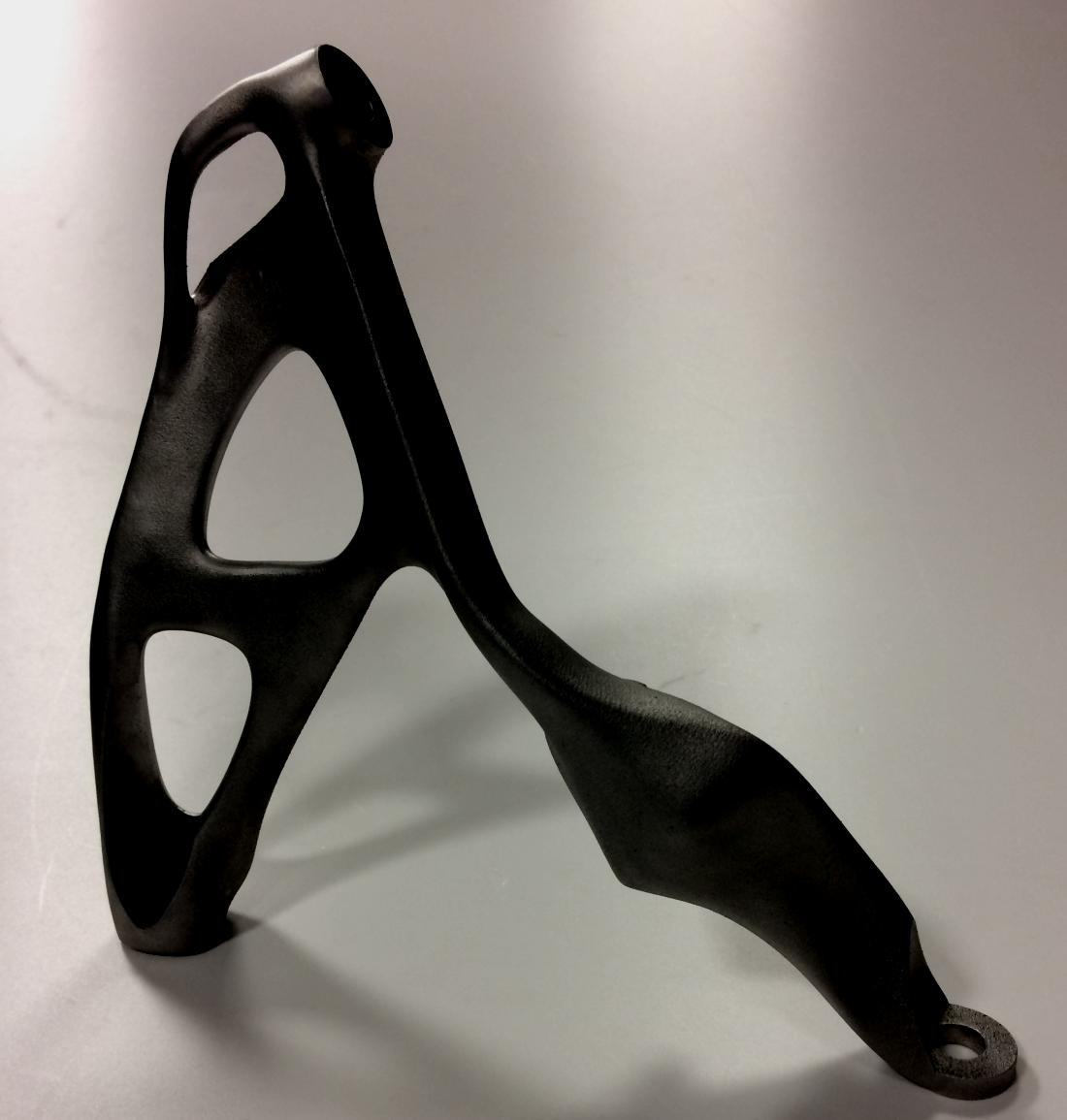
Since 3D printing is still a relatively recent technology, there is quite a bit of leeway to explore and test new applications. The next step for Thales Alenia Space will be to make larger and increasingly complex parts. Among the developments under way is a program to integrate multiple functions – mechanical, thermal and RF for instance – in a single part. Thales Alenia Space is also working on ways to expand the range of materials that can be used with this technology. All Thales Alenia Space-built satellites will eventually incorporate parts made by additive manufacturing.
Innovation and Digital Transformation:
Additive manufacturing is an integral part of the company’s general strategic approach based on innovation and digital transformation, embodied in the Factory of the Future concept. In the fiercely competitive communications satellite market, manufacturers have to produce “more, faster and cheaper”. New technologies such as 3D printing have become a key to increasing the satellite production rate, against the background of a quickly changing industry. The Factory of the Future is designed to incorporate state-of-the-art and cost-competitive technologies in a company’s production organization, fully reflecting the digital transformation. Additive manufacturing, robots and cobots, Industry 4.0, virtual and augmented reality… That sometimes overused buzzword, innovation, has really come into its own at Thales Alenia Space!
Copyrights:
Artistic views: ©Thales Alenia Space/Briot/Initium3d
Photos: ©Thales Alenia Space
Movie: ©Thales Alenia Space/Master Image Programmes/Films06